What Are The Parts Of A Shipping Container?
The giant steel box that was used to house goods and cargo on long journeys overseas can be taken apart. Each part of the container serves a specific purpose and the moment you remove one facet, the container loses its functionality. However, that doesn’t mean you shouldn’t dismantle it so you can use the container for other purposes or use the materials on their own.
There are six parts that make up a shipping container:
- Floor
- Corner posts
- Side walls
- Roof
- Cross members
- Horizontal support rails
Usually plywood is used for the floor because it will not warp when exposed to moisture and the wet environment of ocean travel. The rest of the container is made of strong steel and metal materials. Each part plays a role in how the container handles weight.
A container must also remain flexible to deal with the loading and unloading process. This process is done by crane because the containers need to be moved from boat to land or rail quickly and carefully, to ensure that the goods inside are delivered on time and without damage. Although, if you were to accidentally drop a shipping container, they are tough and will not break.
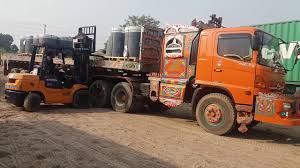
What’s the difference between watertight and waterproof?
A container that is watertight is made with materials that do not allow water to enter it. Watertight containers can also lock water in to allow for the transportation of liquid. Conversely, a container that is waterproof means that it is coated in a substance that makes it resistant to water. However, a container that is simply waterproof and not watertight can still let water in. For instance, if rain hits the outside of a waterproof container, there will be no damage. But if rain seeps into a waterproof container, its contents will incur damage.
Are shipping containers affected by condensation?
Older watertight containers can be affected by condensation if they are placed on damp ground and subject to temperature variations. The dampness of the soil will penetrate the metal container and create condensation inside it. Nevertheless, the corrugated construction and the paint used on modern containers reduce the amount of condensation that accrues so that it’s basically non-existent. If you do have an older watertight container, you can use a venting system or open the door on a dry day to force the condensation out.
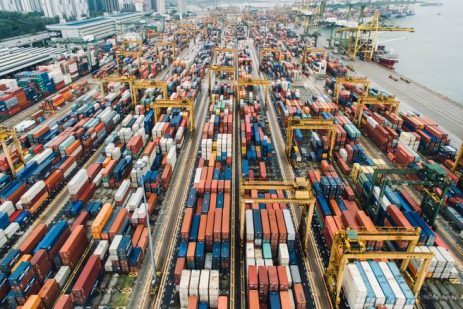
Are Containers Fireproof?
Containers are made out of steel, which is a fire resistant material. Therefore, a container would only catch fire in very extreme cases, like if the container was already carrying a large amount of flammable materials. If, for whatever reason, a fire was to start inside of a container, the container would be able to prevent the fire from escalating. Containers are airtight, therefore the fire would extinguish itself once it has used up all of the oxygen inside the container. While the inside of the container in question would be damaged, at least the fire would have been prevented from spreading.
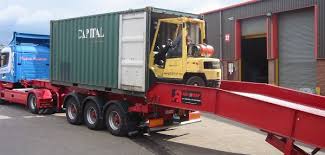
What vehicles can you load and unload using forklift trucks?
Forklift trucks provide (secure) the efficient loading and unloading of straight trucks, tractor trailers, railway cars and elevators.
What should you do to load (unload) vehicles using a forklift truck?
- Keep forks pointed downhill when traveling without a load on a ramp.
- Keep forks pointed uphill when traveling with a load on a ramp.
- Stay clear of edges of docks, rail cars or ramps. Have edges clearly marked.
- Do not tow or push railway cars or trucks with a forklift.
- Do not operate forklifts inside vehicles for long periods without ventilation.
- Make sure that the dock plate is properly secured and can support the load before driving over it. (Load weight should be clearly marked.)
- Drive carefully and slowly over the plate. Do not spin wheels.
The Importance of Loading Dock Layout
A loading dock is a necessity for nearly any kind of business or warehouse that ships or receives goods, although many people are unaware of its design and function. We at Beuschel Sales get a lot of questions from our customers about what the best kind of dock layout is in order to maximize efficiency and safety. This can vary based on any number of things, including available space for the truck to reach the loading dock, the slope of the dock approach, the loading-dock door size, bumper and dock seal projections, the type of product being loaded/unloaded, the variety of trailers using the dock, and dock height. Does it sound complicated? It can be.
One of the questions we get asked about most frequently is: Why is it necessary to cantilever a dock leveler pit away from a building on a declined approach?
The simple answer (unless you want to learn the geometry involved) is that it’s to keep the top of the trailer from hitting the building. There are several different loading dock designs, and the original is the level-approach loading dock. This type of dock shares the same foundation as the wall of the building it’s attached to. Over the years, in an attempt to keep the trailer from moving away or “creeping” from the dock, declined approaches become more popular, especially in the north where ice buildup under the truck/trailer on approach is a concern and increases the chance of a trailer moving. With a declined approach application, it is necessary to cantilever the dock leveler pit away from the foundation wall to keep the top of the trailer from hitting the building wall.
Most approaches to the loading dock are not completely level, of course, but the steeper the incline or decline, the more problems you’ll have. The tilt of the trailer back to the building will create a flow of water into the building when it rains, it basically becomes a 53’ long 8’ 6” wide rain gutter flowing back into the building. Inclines or declines that are too steep will also create safety hazards for the fork truck driver to be able to climb or stop on the incline with the product.
It’s important to know both your loading dock settings and the fleet of vehicles that will use it in order to avoid both accidents and damage. Many businesses feel that having any loading dock equipment and design is good enough. They overlook the additional safety that proper equipment and design chosen for the approach, the dock, and the vehicles provides.